2. Soluciones de ensamblaje
Los expertos en ensamblaje, como los de Desoutter, han desarrollado una amplia gama de soluciones de ensamblaje con cable y con conexión wifi diseñadas para garantizar que el ensamblaje de vehículos eléctricos (NEV) sea seguro, eficiente, flexible y trazable. Varios rangos de herramientas de apriete con transductor, por ejemplo, están equipados con sensores de par y ángulo para asegurar que la unión se aprieta utilizando los parámetros correctos.
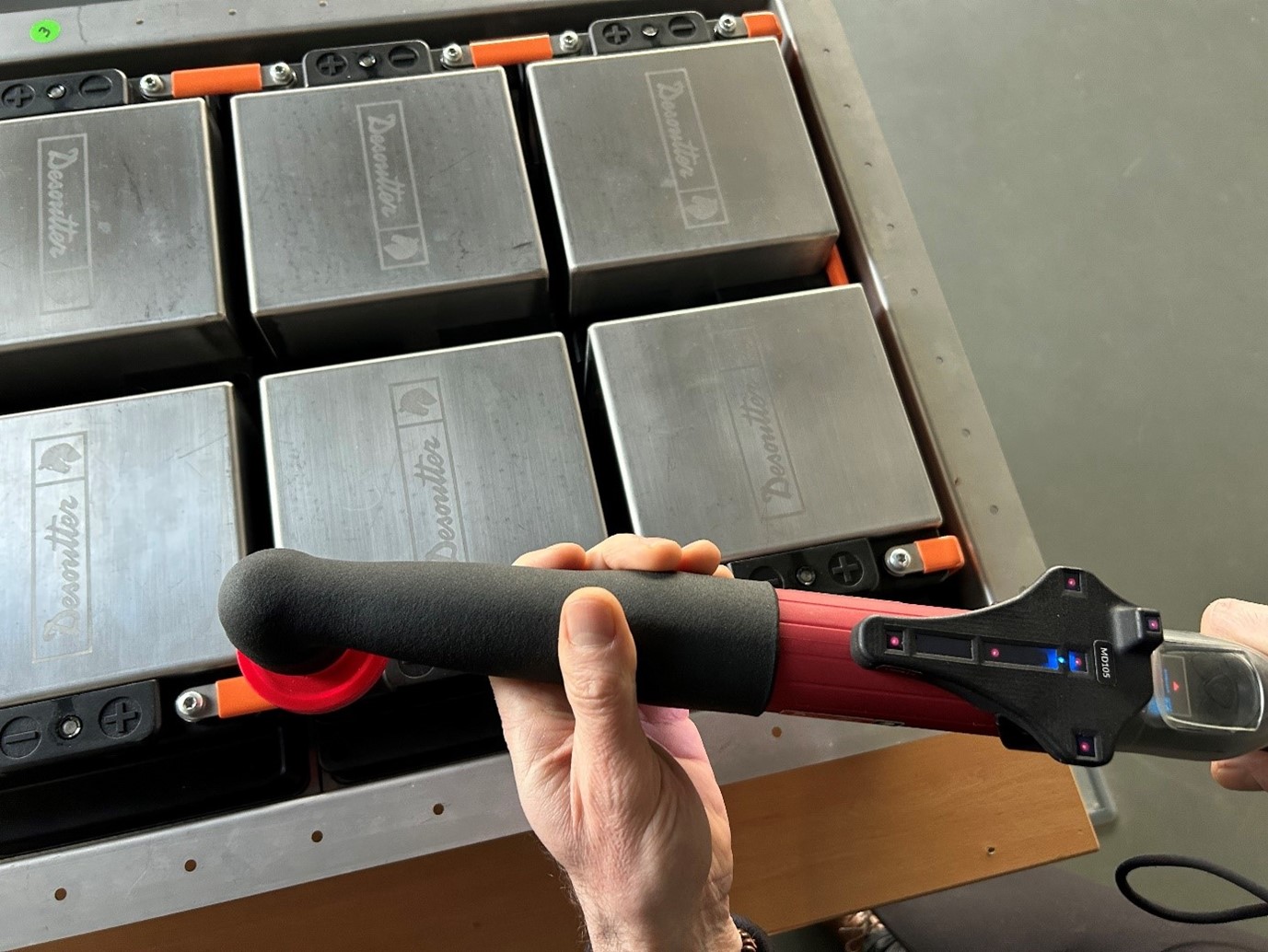 |
|
Estas herramientas cuentan con adaptadores aislantes y pueden estar equipadas con protecciones para minimizar el riesgo de contacto con voltajes peligrosos, siendo ideales para la conexión de barras colectoras de potencia. Estos productos de protección para los trabajadores han sido probados y aprobados por Dekra según las normas IEC 60900:2018, IEC 60664-1 y EN 60745-1. |
El apriete secuencial para un control total de calidad puede lograrse mediante plataformas de asistencia para el trabajador:
Software de control de procesos, que guía al operador a través de cada etapa del proceso de apriete. Una aplicación típica en NEV es el aseguramiento de la tapa del paquete de baterías, que requiere un apriete sincrónico para garantizar que el sellado entre la tapa y la carcasa inferior sea hermético.
Sistemas de guiado para el operario que combinan guiado láser y tecnología de captura de movimiento están siendo introducidos para respaldar los principios de Poka Yoke y lograr procesos de apriete sin errores. Estos sistemas eliminan por completo los errores del operador, asegurando que ningún tornillo se omita y que siempre se aplique el par correcto.
Soluciones multihusillo, permiten un ensamblaje sincrónico con el par definido: por ejemplo, garantizando que los módulos de los paquetes de baterías se monten con una fuerza de apriete adecuada para eliminar el asentamiento, evitando que los componentes ensamblados se deformen. Las soluciones multihusillo mejoran significativamente los tiempos de ciclo, especialmente cuando se combinan con un alimentador automático de tornillos.
El intercambio de datos de apriete con el sistema de control superior puede garantizarse mediante un smart hub combinado con herramientas inalámbricas. Por ejemplo, cuando un sistema de control transmite los parámetros correctos para la tarea de apriete a realizar, recibe a cambio los resultados del apriete para trazabilidad y documentación.
El rendimiento, la calidad y otros parámetros del ensamblaje NEV pueden ser monitorizados constantemente mediante tableros de análisis de datos. También existe la opción de enviar alertas en tiempo real a teléfonos inteligentes. El análisis de datos detallado con KPIs en tiempo real para rendimiento, calidad y disponibilidad permite la rápida identificación de tendencias de producción para mejorar continuamente la eficiencia.
El análisis de grandes datos también puede respaldar la trazabilidad total. En el pasado, los datos de trazabilidad se almacenaban por separado y no eran fáciles de consultar. Las nuevas soluciones de big data pueden recopilar y analizar datos en todos los niveles de producción y desde cualquier dispositivo o sistema, independientemente del fabricante. Los informes automatizados permiten a fabricantes y proveedores acceder a conjuntos de datos complejos en cualquier momento para obtener información sobre prácticamente cualquier aspecto de la calidad y la producción, incluyendo:
- % de piezas NOK / estación
- tiempo medio por pieza / estación
- % de errores de ensamblaje / estación
- alertas de control de proceso
- alertas de batería vacía de herramientas
- alertas de piezas faltantes
Estos datos valiosos no solo identifican áreas para mejorar continuamente la eficiencia de producción y reducir costes, sino que también reducen considerablemente la probabilidad de retiradas de productos costosas y perjudiciales.