How to avoid recall for electric vehicle?
The impact of Product Recalls on the Electric Vehicles and the Solutions for Assembly. Solutions for OEMs exists to ensure high quality tightening: Positionning system Camera, Data Analytics, Traceability.
Vehicle recalls by the manufacturers
The electric vehicles industry has witnessed a significant rise in recent years with governments around the world setting ambitious targets for reducing carbon emissions and promoting clean energy. More and more people are choosing electric cars as their preferred mode of transportation. However, as with any industry, the EV (electric vehicle) sector faces its own set of challenges. One such challenge is product recalls, which have become a major concern for OEMs and for Tiers Suppliers.
Download our white paper for more information :
Challenges posed by Product Callbacks
Product recall check can be devastating for an OEM's and Tiers brand, and in the highly competitive EV market, it can easily lead to a loss of market share. This is not only a costly process, but it can also be devastating for the manufacturer's brand reputation. Callbacks can be initiated due to various reasons, such as faulty parts or engines randomly starting. For electric vehicles in particular, where fully charged batteries with high voltage pose a potential threat, callbacks can become an even greater concern.
In 2021, a leading battery maker agreed to pay a US automaker nearly $2 billion to cover the cost of a recall involving batteries in 141,000 electric cars. In China, close to a quarter of the total 199 recall events recorded last year were for NEVs (new energy vehicles).
For Hyundai, the recall will cost $900 million. Still, a recall costing more than $11,000 per vehicle is extremely rare.
According to Mike Held, a director in the automotive and industrial practice at AlixPartners, a global consulting firm, the average cost of an auto recall over the last 10 years was about $ 500 per vehicle. Source : Hyundai's recall of 82,000 electric cars is one of the most expensive in history | CNN Business.
"Overall, battery safety and durability will be increasingly important if auto companies want to avoid some of the large battery-recall costs that have befallen the consumer-electronics industry."
Mike Held
Solutions to Avoid Product Callbacks:
To avoid callbacks and maintain process quality, OEMs and Tiers need smart tools that can detect any non-conformances (NOKs) during the tightening process, they require technology that can detect the position and number of each tightening wich ensures that no tightening is missed and the correct pattern is applied. This level of automation can help reduce human error and ensure a consistent and reliable process.
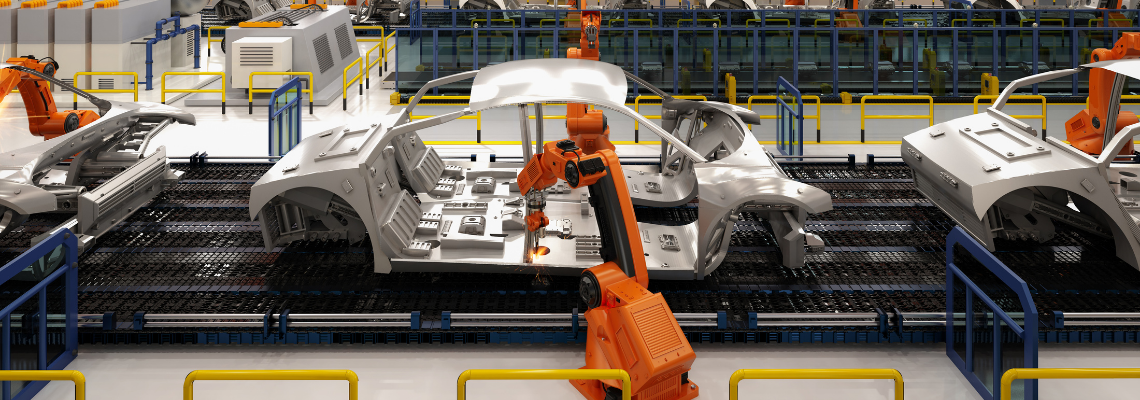
How to identify weaknesses in the process:
|
Real-Time Location System integrated with nutrunner, to make sure that all screws are tightened in the right place, at the right time. Based on infrared technology, nexonar RTLS can provide precise tracking of where manufacturing actions are performed by different assets and personnels, which can significantly reduce the risk of recall. |
|
Analytics platform that transforms data. It offers three distinct ways which users can interact with their data to derive optimum value. Solutions such as DeMeter can answer data challenges. |
|
Process control systems solutions will guide operators to a better assembly solution. These solutions offers step-by-step digital instructions to help avoid human error and callbacks. Pivotware is a good match for these problems. |
|
First class tightening quality. Will ensure high precision between tools and data exchange. With an easy pairing, it takes only a few seconds to exchange the tools in the running line, making it easier to use capable, regularly maintained tools. Connect smart hub is one possibility to consider. |
With these systems many recalls, such as when suppliers recall components, can be avoid. If the supplied assemblies are also recorded by serial number and documented in the birth certificate, a manufacturer can address customer's concerns in a targeted manner without having to recall production for several weeks.
How can birth certificate seamless traceability?
For electric vehicles, it is crucial to have a birth certificate and a good traceability system that records every process step conducted by workers. Along with the VIN (vehicle identifier number), this can help identify which part of the car is of concern. This solution can help maintain process quality and avoid costly errors during production.
Instead of recalling the entire production line, manufacturers can identify the affected assemblies using their unique serial numbers and contact only those customers who bought products containing the defective assemblies.
This targeted approach saves time and resources that would have been spent recalling the entire production line from production to distribution to end-users. It also enhances customer relationships by minimizing the impact of product defects on customers who didn't purchase products with the defective part.
Conclusion
With the rise of the EV industry, product callbacks have become a major concern for OEMs and Tiers. They can lead to costly errors, damage brand reputation, and result in a loss of market share. However, by adopting smart tools, detecting non-conformities during tightening, and ensuring a robust traceability system is in place, OEMs can avoid costly errors and maintain process quality. For more information on how to avoid callbacks and improve process quality, consult your local Desoutter representative.
Discover our whitepaper: Safe electric car assembly
Sustainability is the priority of governments across the globe and they have played a role in educating the public. One key message is that CO² is linked to the combustion engine. NEV manufacturing requires different designs and production processes. Sometimes this means different requirements from the tools being used, and in particular, safety for the users.